The next project has been realized by our company is diaphragm compressor DC 2-62/6-100-H2 for hydrogen (H2).
Project information:
Customer is manufacturer of polyethylene terephthalate and terephthalic acid.
Delivery date is 2019.02
Description: hydrogen oil-free diaphragm compressor DC 2-62/6-100-H2 to compress the high purity H2 (99.99%).
Technical parametres are indicated below:
Model | DC 2-62/6-100-H2 |
Compressor type | Diaphragm oil-free compressor |
Inlet pressure (bar g) | 6 |
Outlet pressure (bar g) | 100 |
Inlet gas temperature (°С) | -10…+40 |
Pressure dew point (°С) | –
gas is dry |
Capacity (Nm3/h) | 62 |
Gas | H2 (99.9%) |
Cooling | water |
Cooling water temperature (°С) | + 1 … + 32 |
Cooling water capacity (m3/h) | 1.5 |
Cooling water pressure (bar g) | ≤ 6 |
Ambient temperature (°С) | + 1 … + 45 |
Motor power 400/3/50 (kW) | 18.5 |
Real power consumption (kW) | 12.4 |
Control panel | Included as separate unit |
Implosion protection (by motor) | 1Exd IIC T4 |
Dimensions LхWхH (мм) | 1940х1300х1230 |
Weight (kg) | 1750 |
Compressor description
DC 2-62/6-100-H2 is oil-free diaphragm compressor for hydrogen (H2).
It’s 2 stage compressor.
Cooling: water (air cooling is option under request).
Our compressor was delivered for replacement for the old 1987 year of building compressor from Burton Corblin
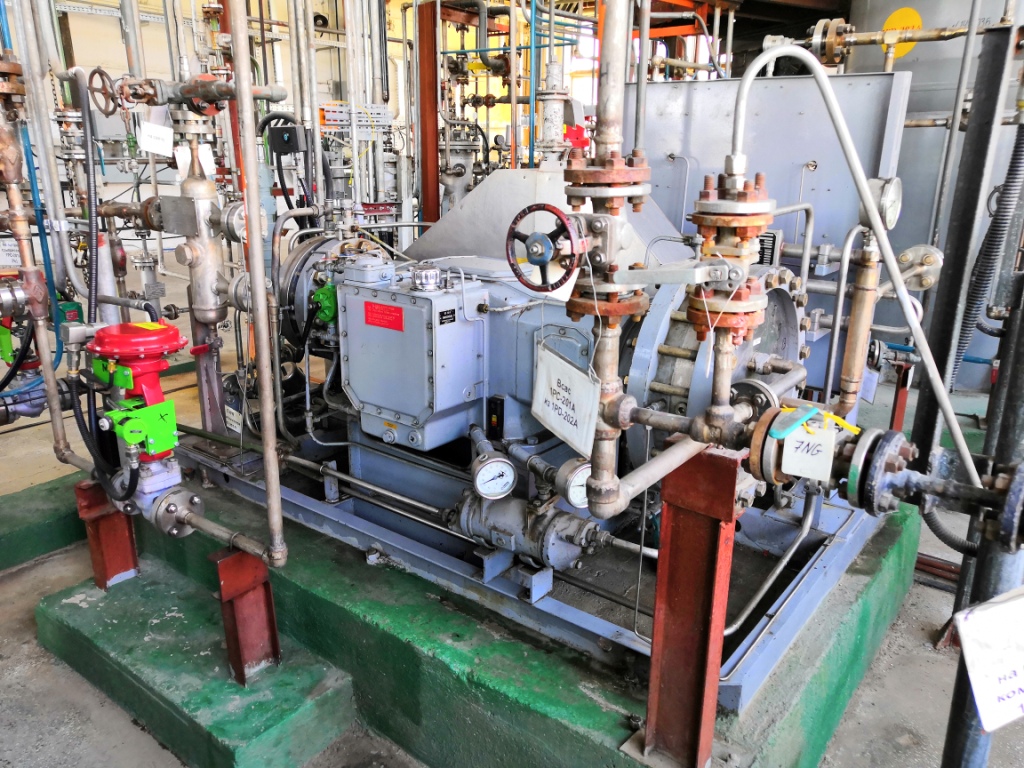
Burton Corblin compressor
Additionals photos
Compressor’s scope of supply
The following was included:
- 2 stages compressor block
- cranck case breather
- electric motor
- motor drive pulley
- v-belts
- drive guard
- inlet gas port
- baseplate with 4 holes
- manometres (6 pieces are installed on compressor + 6 pieces as spare set)
- inlet gas pressure sensor
- outlet gas pressure sensor
- 1st stage oil pressure sensor
- 2nd stage oil pressure sensor
- crank case oil pressure sensor
- water pressure sensor
- inlet gas temperature (resistance temperature detector)
- outlet gas temperature (resistance temperature detector)
- gas temperature after 1st stage (resistance temperature detector)
- gas temperature before the 2nd stage (resistance temperature detector)
- water temperature (resistance temperature detector)
- water flow switch
- non-return valve for final gas delivery (resistance temperature detector)
- safety valve after the 1st stage and for final gas delivery
- interstage and final gas cooler
- two (for 2 stage compressor) pressure relays to control the diaphragm rapture
- tubes “inside” compressor
- terminal box
- electrical connections to terminal box “inside” compressor
- control panel as separate unit for installation in the safe area
- additional control device with Start/Stop/Emergency stop buttons + Green/Red/Yellow lamps for installation with compressor in explosive zone
- water cooling
- manual oil pressure setting in compressor
These options were added:
- inlet / outlet gas valves
Compressor was delivered as totally accembled unit, tested and ready for the comissioning.
Control panel
Compressor is equipped with control panel for safety area installation.
Compressor panel has the operator screen and all necessary laps and buttons for the safety operation.
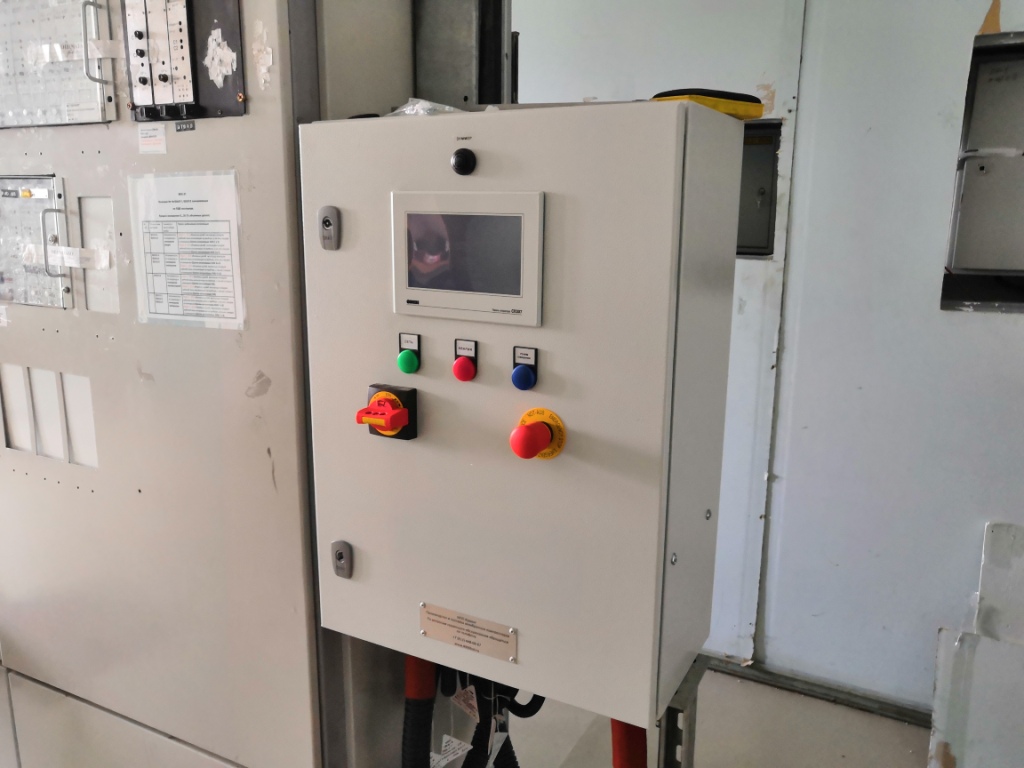
Control panel for H2 compressor
Also additional control device with Start/Stop buttons + Green lamp for installation with compressor in explosive zone is also included.
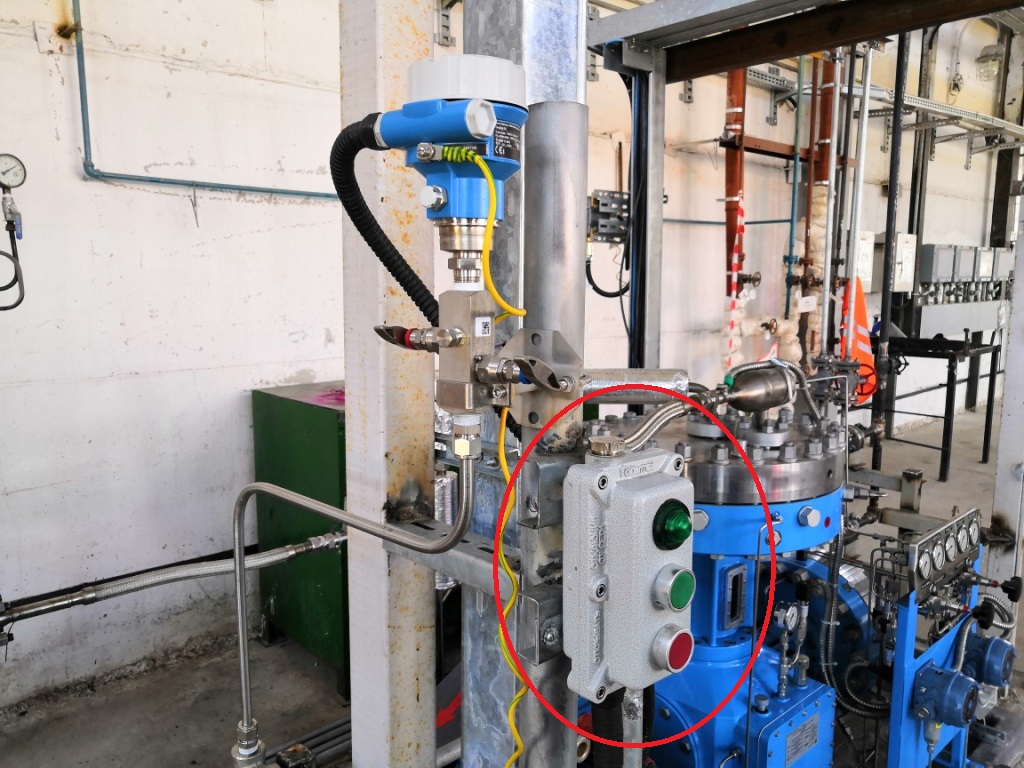
Additional control device
It’s the old version.
And now we include this device with Start/Stop/Emergency stop buttons + Green/Red/Blue lamps:
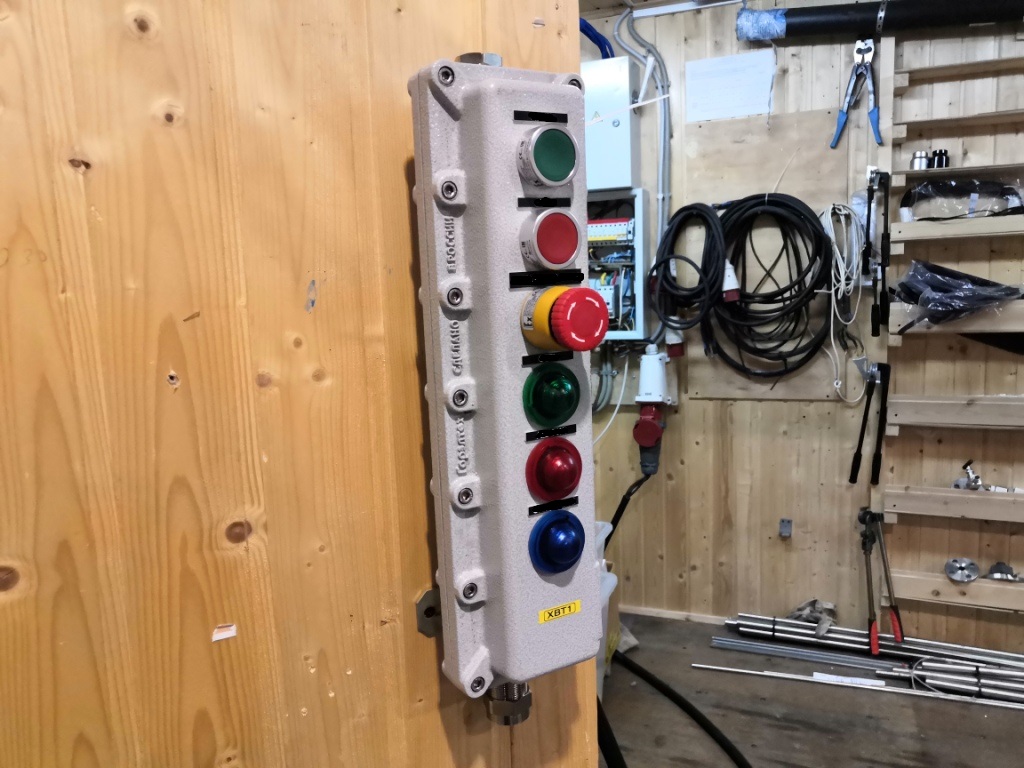
Control Start/Stop device
Gauge panel
Gauge panel is placed on the front part of compressor.
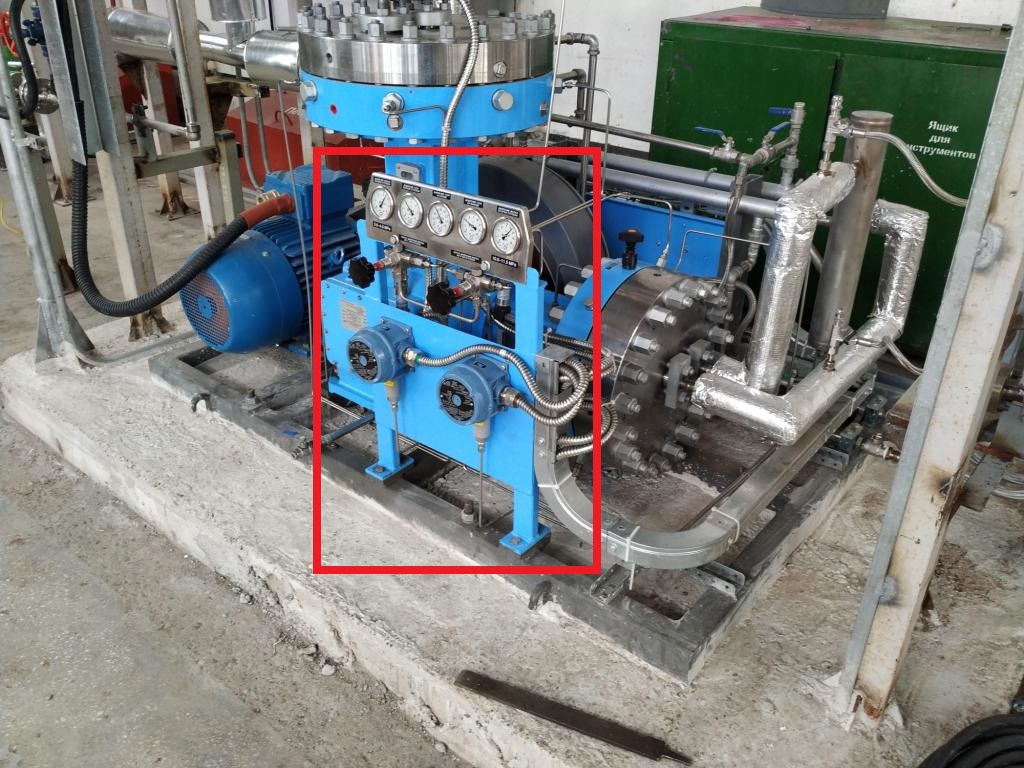
H2 compressor gauge panel
18.5 kW motor is installed.
That’s all.
If you need compressor for hydrogen (H2) help please don’t hesitate to contact us.
You can send request and will answer during the one working day.
Best regards,
Konstantin Shirokikh