Probably hydrogen is the most discussed gas in nowdays.
It’s explosive and, at the same time, it’s one of the simplest gases.
The famous author Jules Verne has mentioned about hydrogen as interesting gas and as gas of the future in his novel “The Mysterious Island”, which was published in 1875.
Elon Musk, in the opposite, calls the Hydrogen “fool sells” insted of “fuell cell”.
But…
Anyway hydrogen is very interesting gas and has a lot of applications.
We can offer oil-free diaphragm compressors for high purity H2 with purity 99% – 99.9995% or less for different industries like H2 fuell stations, chemical industry, aerospace industry and others.
The model range
We have one or two stages compressors with one, two or three cylinders with vertical, L or opposite design.
Standard pressure range is 2-3 bar g … 1000 bar g and more.
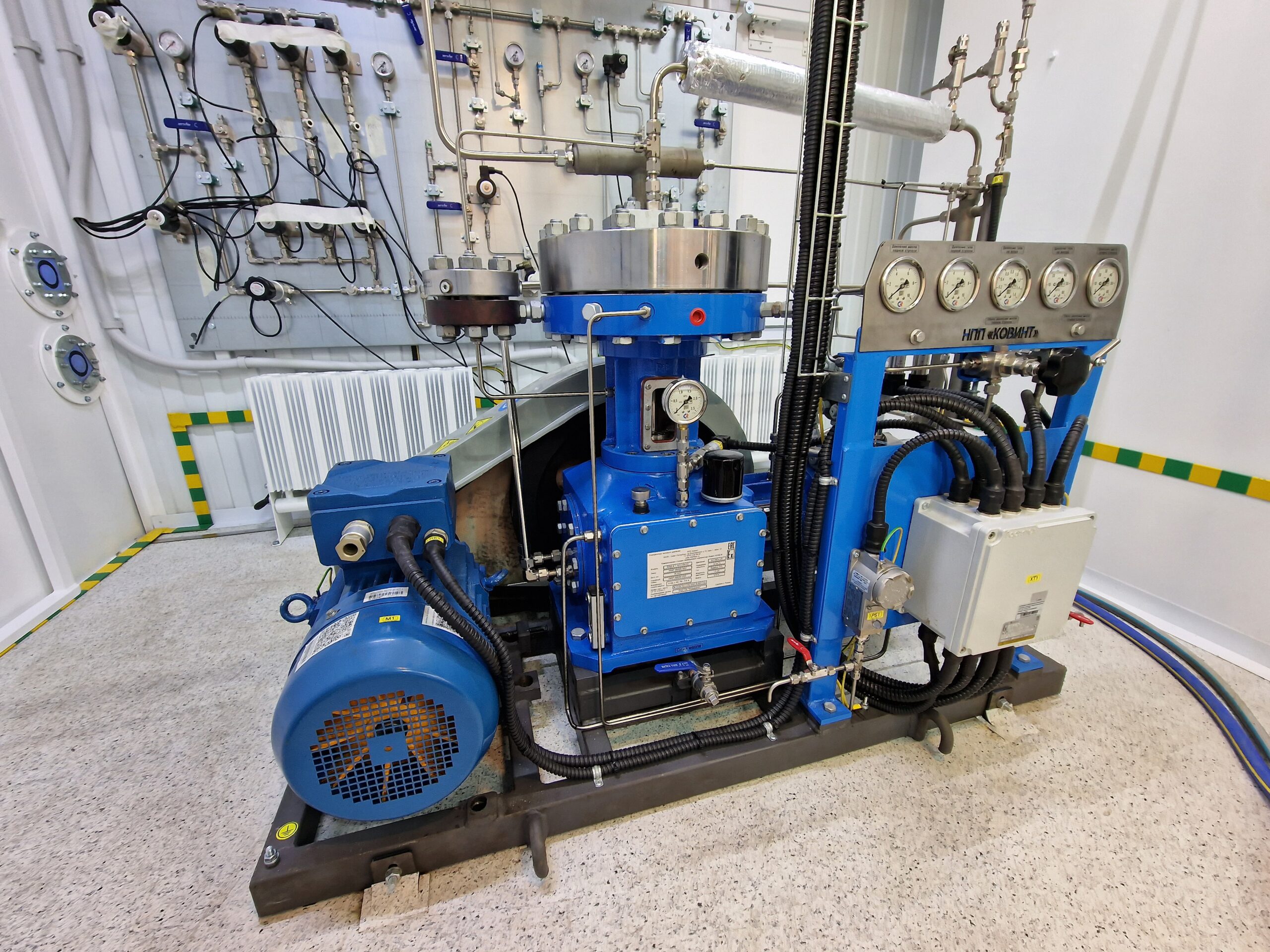
Compressor for hydrogen 400 bar – 10 Nm3h – hydrogen fueling station
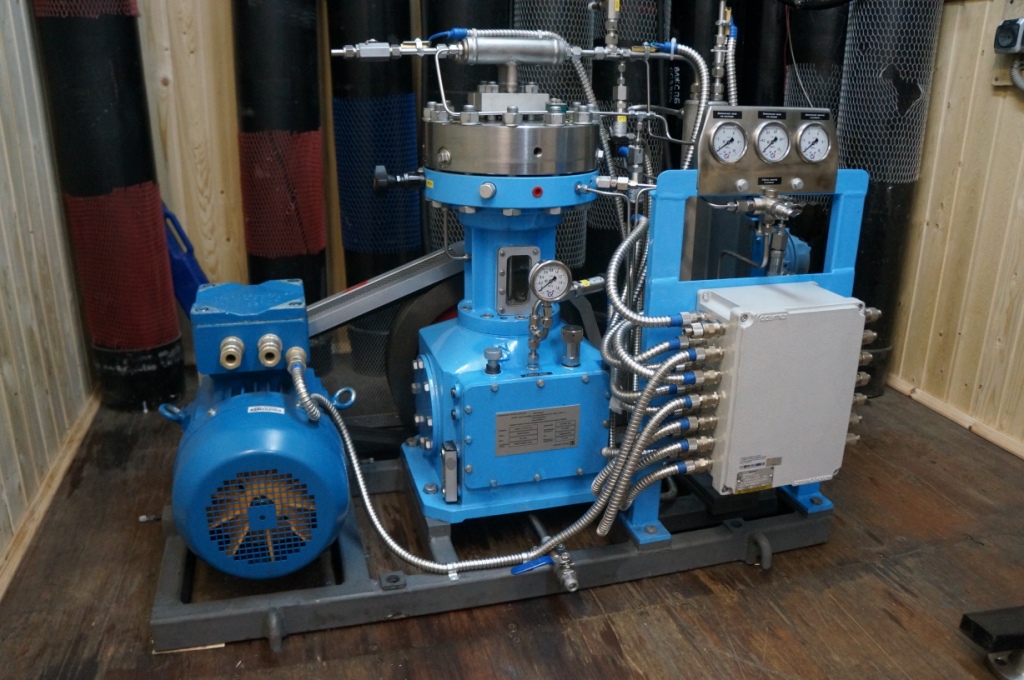
One stage vertical design Hydrogen compressor
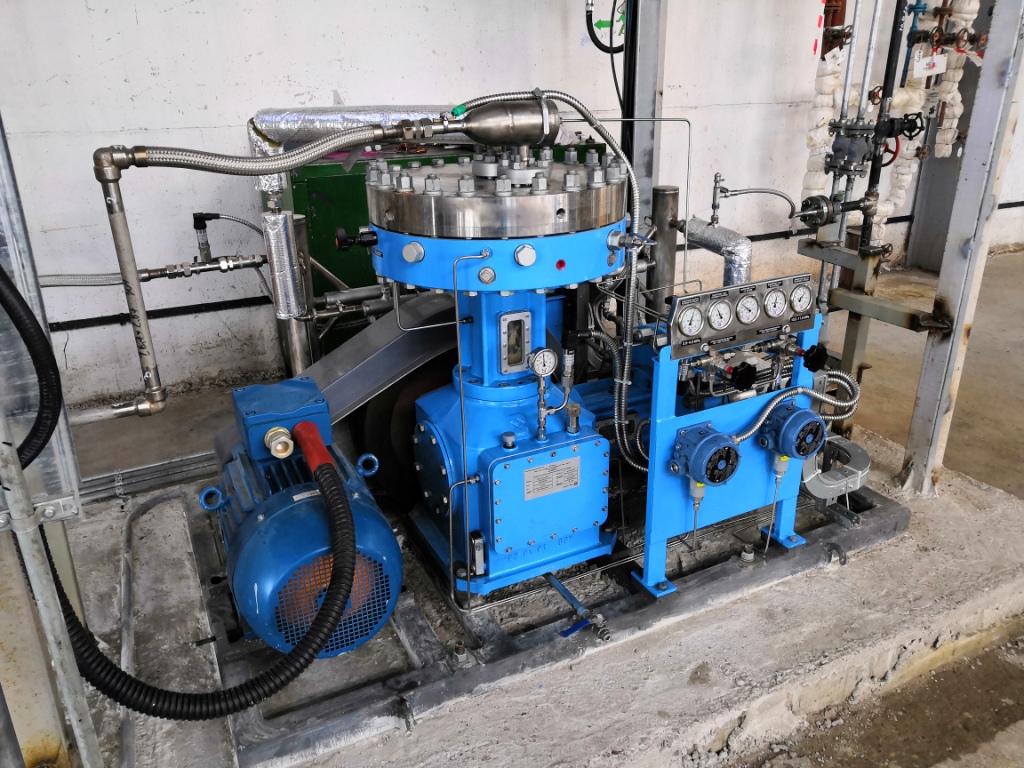
Two stage L-design Hydrogen compressor
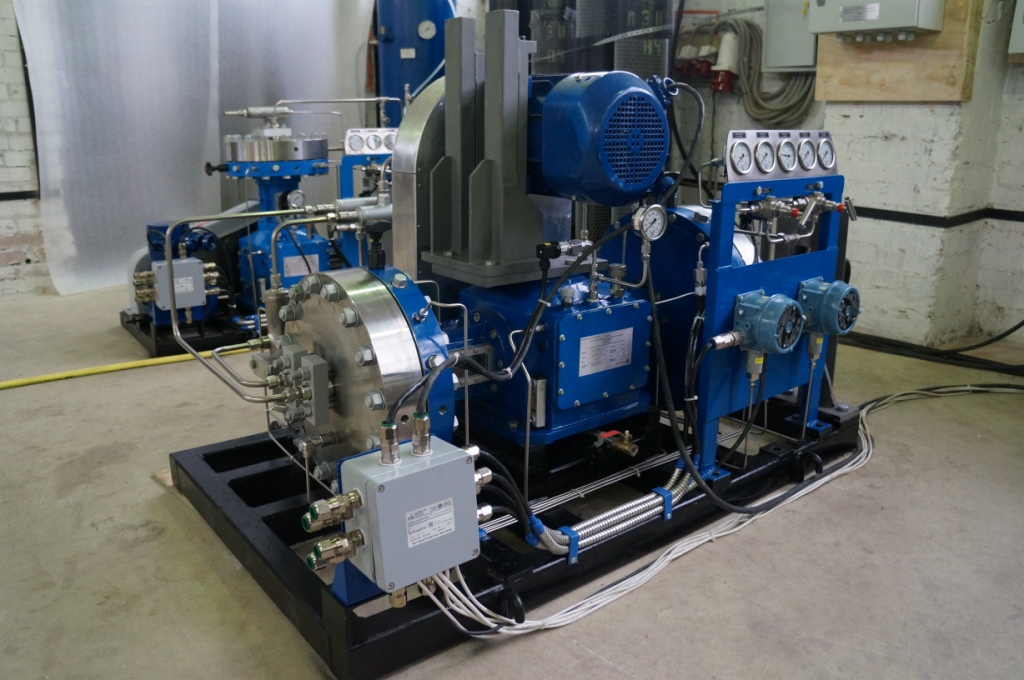
Two stage opposite design Hydrogen compressor
The standard scope of supply
Each standard compressor has:
- one, two or three stages compressor block
- crankcase breather
- electric motor
- motor drive pulley
- v-belts
- drive guard
- inlet gas port
- baseplate with 4 holes
- manometers (6 pieces for 2 stage compressor are installed on compressor + 6 pieces as spare set)
- inlet gas pressure sensor
- outlet gas pressure sensor
- crank case oil pressure sensor
- inlet gas temperature (resistance temperature detector)
- outlet gas temperature (resistance temperature detector)
- non-return valve for final gas delivery
- safety valve after the 1st stage and for final gas delivery
- interstage and final gas cooler
- two (for 2 stage compressor) pressure relays to control the diaphragm rapture
- tubes “inside” compressor
- terminal box
- electrical connections to terminal box “inside” compressor
- control panel as separate unit for installation in the safe area
- additional control device with Start/Stop/Emergency stop buttons + Green/Red/Yellow lamps for installation with compressor in explosive zone
- water cooling
- manual oil pressure setting in compressor
and available options:
- air cooling
- oil pressure sensors to control oil pressure inside the compressor heads (compressor’s stages)
- automatic oil pressure settings in compressor without operator activities
- automatic unloader/drainage system
- inlet / outlet gas valves
- container installation or special design compressors
Each compressor is delivered as totally assembled unit, tested and ready for the commissioning.
Control panel
Each compressor is equipped with control panel for safety area installation.
Compressor panel has the operator screen and all necessary laps and buttons for the safety operation.
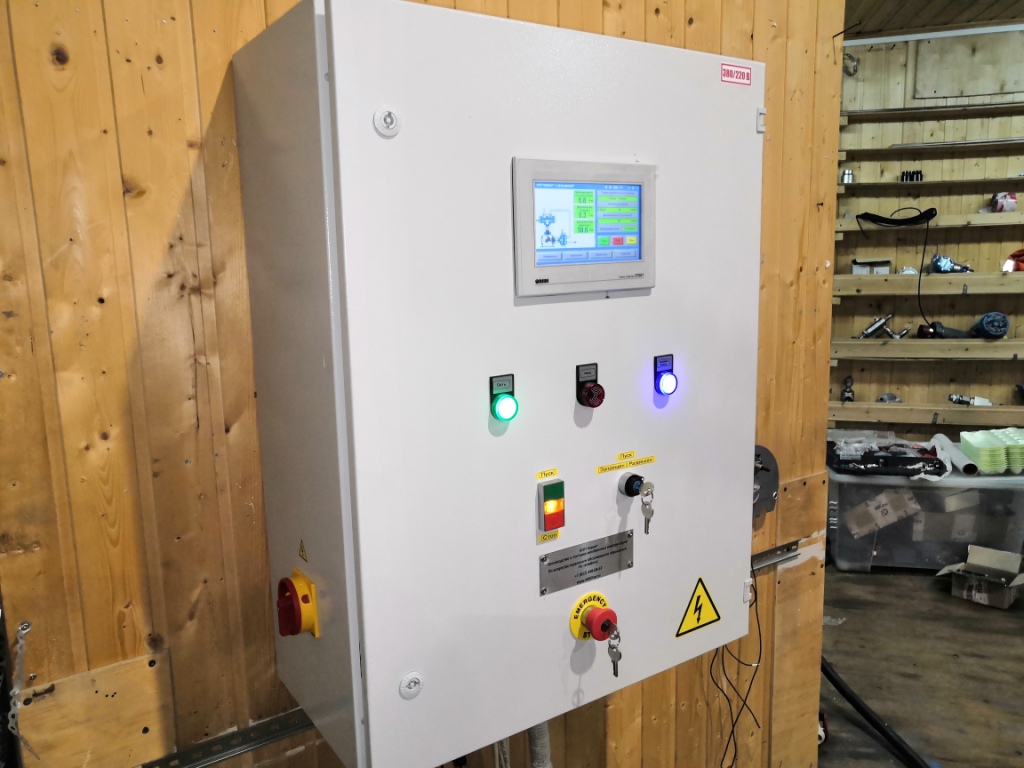
Control panel for hydrogen compressor
Additional control device
Additional control device with Start/Stop/Emergency stop buttons + Green/Red/Blue lamps for installation with compressor in explosive zone is also included.
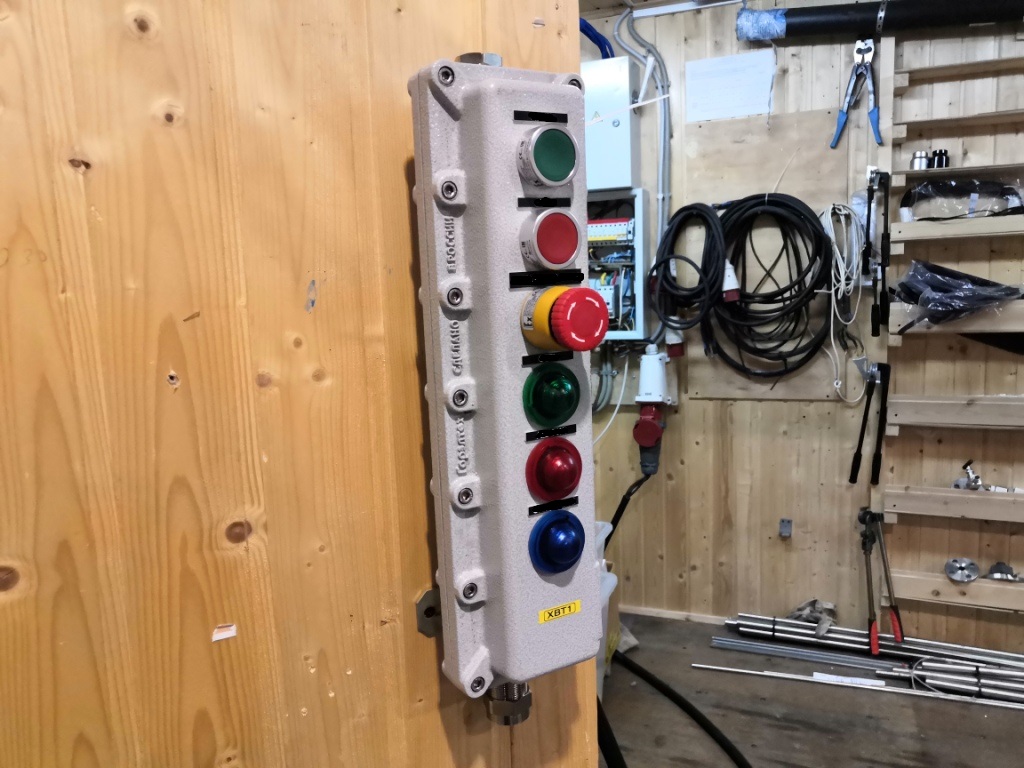
Control Start/Stop device
Special design
Sometimes we meet not standard tasks.
For example one customer asked us a couple years ago to make compressor with special shelter for outside installation and for ambient temperature range -40…+40 0С.
They didn’t have enough place to install the standard 20 feet container, that’s why we offered this solution:
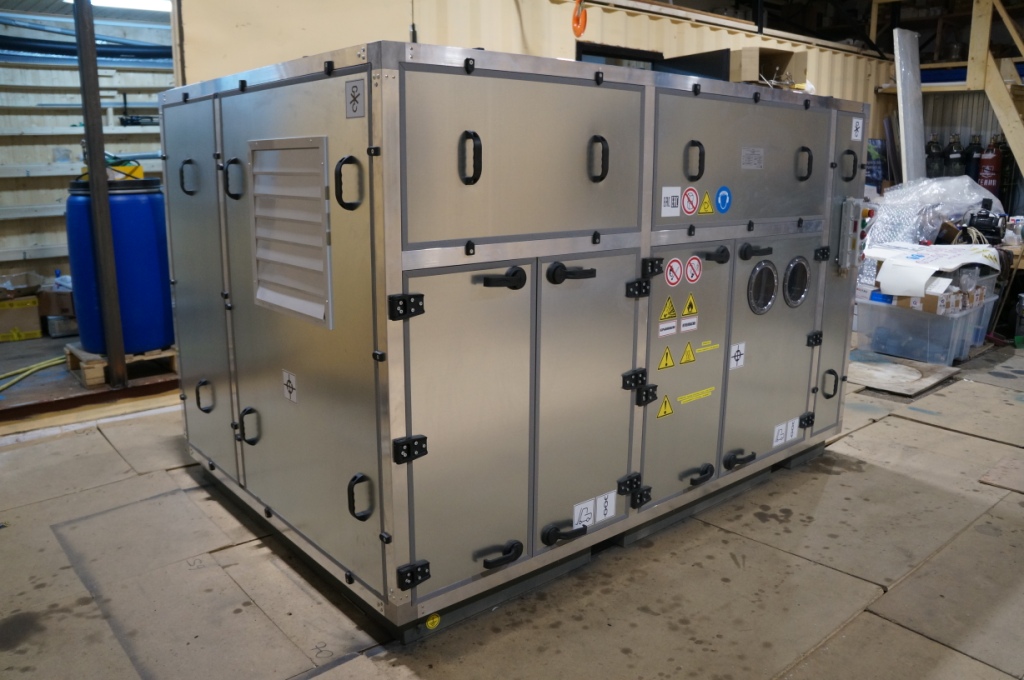
Compressor for hydrogen with special shelter
Note:
This solution is not perfect for winter time.
It’s too hard to make maintenance or repair.
Our recommendation is to install compressor inside the standard 20 feet container.
Hydrogen compressors for Hydrogen fuel stations
Also I would like to show our expirence with hydrogen fuel stations.
First example is with 30 Nm3/h compressor and pressure range 10 – 400 bar.
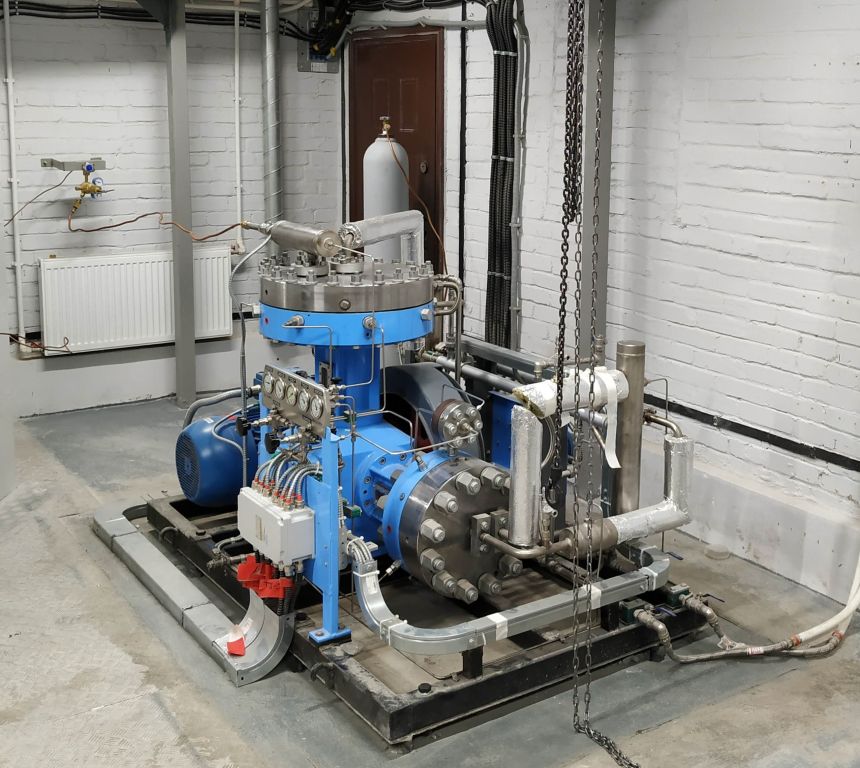
Hydrogen compressor for the hydrogen fuel station 30 Nm3/h / 10 – 400 bar g
The second is 450 bar g compressor as a part of hydrogen fuel station:
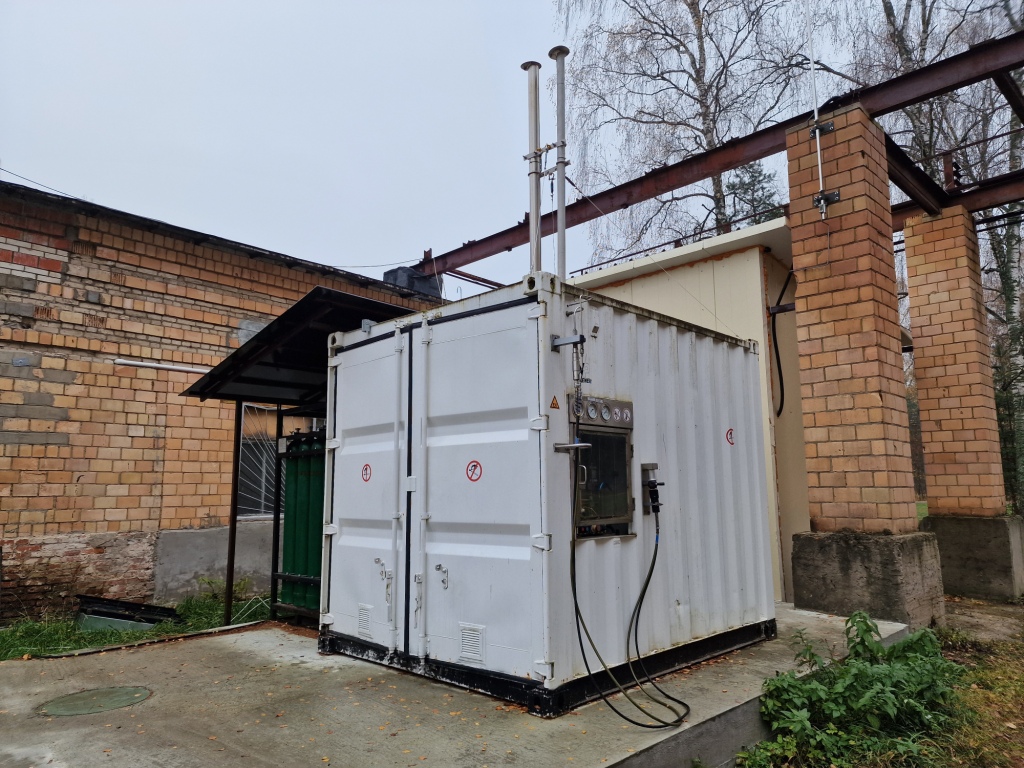
Hydrogen compressor station
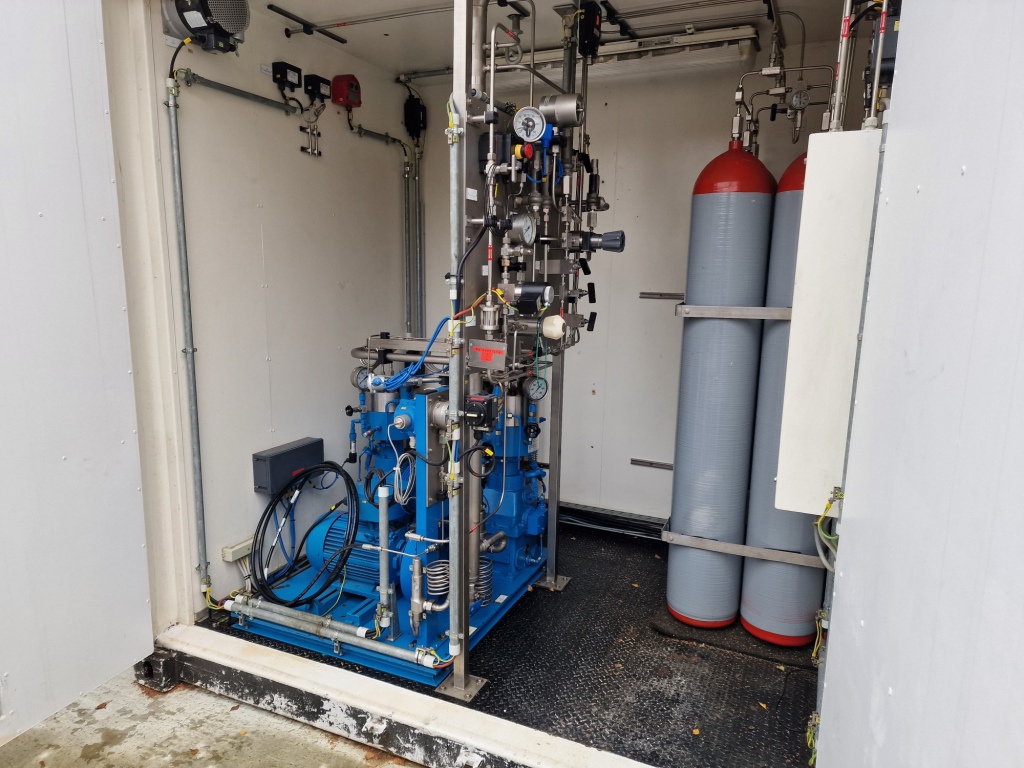
Hydrogen compressor station
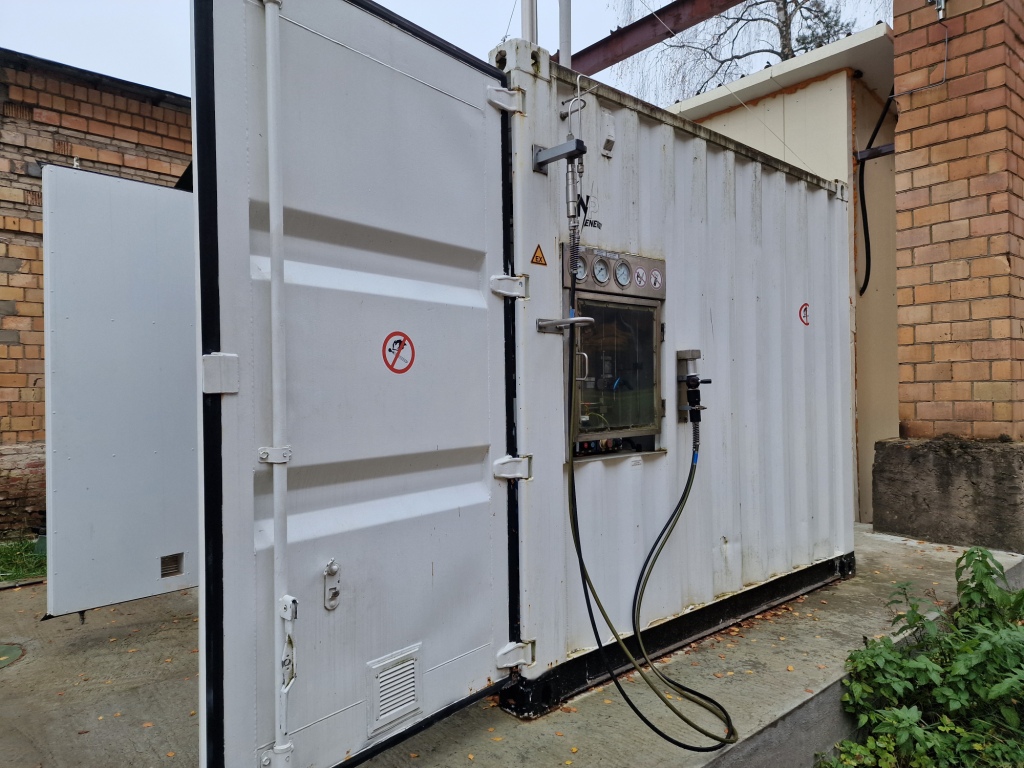
Hydrogen compressor station
Compressors models
The most popular models are indicated below.
All models are indicated just for example
If you didn’t find the model you need please send inquiry to us and we will find solution for you.
Model | Q
Nm3/h |
Pressure
inlet bar g |
Pressure
outlet bar g |
Motor
kW |
Weight
kg |
DC 1-5.5/0.1-90-H2 | 5.5 | 0.1 | 90 | 3 | 550 |
DC 1-5/0.01-150-H2 | 5 | 0.01 | 150 | 3 | 550 |
DC 1-5.5/0.1-165-H2 | 5.5 | 0.1 | 165 | 3 | 550 |
DC 1-4/0.1-200-H2 | 4 | 0.1 | 200 | 3 | 550 |
DC 1-6/0.2-12.5-H2 | 6 | 0.2 | 12.5 | 3 | 550 |
DC 1-12/0.2-12.5-H2 | 12 | 0.2 | 12.5 | 5.5 | 550 |
DC 1-15/0.5-10-H2 | 15 | 0.5 | 10 | 5.5 | 550 |
DC 1-7/0.5-100-H2 | 7 | 0.5 | 100 | 3 | 550 |
DC 1-6/0.5-150-H2 | 6 | 0.5 | 150 | 3 | 550 |
DC 1-6/0.5-200-H2 | 6 | 0.5 | 200 | 3 | 550 |
DC 1-5/0.5-250-H2 | 5 | 0.5 | 250 | 4 | 550 |
DC 1-3.5/0.5-300-H2 | 3.5 | 0.5 | 300 | 3 | 550 |
DC 1-20/1.5-8-H2 | 20 | 1.5 | 8 | 4 | 550 |
DC 1-10/5-150-H2 | 10 | 5 | 150 | 4 | 550 |
DC 1-12/5-200-H2 | 12 | 5 | 200 | 5.5 | 550 |
DC 1-9/5-250-H2 | 9 | 5 | 250 | 4 | 550 |
DC 1-7/5-300-H2 | 7 | 5 | 300 | 4 | 550 |
DC 1-7/5-350-H2 | 7 | 5 | 350 | 4 | 550 |
DC 1-5/5-400-H2 | 5 | 5 | 400 | 4 | 550 |
DC 1-40/7.5-35-H2 | 40 | 7.5 | 35 | 4 | 550 |
DC 1-15/10-150-H2 | 15 | 10 | 150 | 5.5 | 550 |
DC 1-14/10-200-H2 | 14 | 10 | 200 | 5.5 | 550 |
DC 1-13/10-250-H2 | 13 | 10 | 250 | 5.5 | 550 |
DC 1-10/10-300-H2 | 10 | 10 | 300 | 4 | 550 |
DC 1-15/10-350-H2 | 15 | 10 | 350 | 5.5 | 550 |
DC 1-6/10-400-H2 | 6 | 10 | 400 | 4 | 550 |
DC 1-9/10-400-H2 | 9 | 10 | 400 | 7.5 | 550 |
DC 1-20/15-250-H2 | 20 | 15 | 250 | 5.5 | 550 |
DC 1-7/20-200-H2 | 7 | 20 | 200 | 4 | 550 |
DC 1-9/25-200-H2 | 9 | 25 | 200 | 4 | 550 |
DC 2-40/0.1-10-H2 | 40 | 0.1 | 10 | 11 | 1750 |
DC 2-18/0.1-165-H2 | 18 | 0.1 | 165 | 15 | 1750 |
DC 2-18/0.1-200-H2 | 18 | 0.1 | 200 | 15 | 1750 |
DC 2-50/0.5-10-H2 | 50 | 0.5 | 10 | 15 | 1750 |
DC 2-25/0.5-100-H2 | 25 | 0.5 | 100 | 15 | 1750 |
DC 2-22/0.5-150-H2 | 22 | 0.5 | 150 | 15 | 1750 |
DC 2-20/0.5-200-H2 | 20 | 0.5 | 200 | 15 | 1750 |
DC 2-15/0.5-250-H2 | 15 | 0.5 | 250 | 15 | 1750 |
DC 2-15/0.5-300-H2 | 15 | 0.5 | 300 | 15 | 1750 |
DC 2-50/4.5-160-H2 | 50 | 4.5 | 160 | 18.5 | 1750 |
DC 2-45/5-150-H2 | 45 | 5 | 150 | 18.5 | 1750 |
DC 2-45/5-200-H2 | 45 | 5 | 200 | 18.5 | 1750 |
DC 2-38/5-250-H2 | 38 | 5 | 250 | 18.5 | 1750 |
DC 2-45/6-250-H2 | 45 | 6 | 250 | 18.5 | 1750 |
DC 2-32/5-300-H2 | 32 | 5 | 300 | 18.5 | 1750 |
DC 2-35/5-350-H2 | 35 | 5 | 350 | 18.5 | 1750 |
DC 2-20/5-400-H2 | 20 | 5 | 400 | 15 | 1750 |
DC 2-130/7.5-35-H2 | 130 | 7.5 | 35 | 15 | 1750 |
DC 2-55/7.5-150-H2 | 55 | 7.5 | 150 | 15 | 1750 |
DC 2-47/7.5-200-H2 | 47 | 7.5 | 200 | 18.5 | 1750 |
DC 2-40/7.5-250-H2 | 40 | 7.5 | 250 | 18.5 | 1750 |
DC 2-35/7.5-300-H2 | 35 | 7.5 | 300 | 18.5 | 1750 |
DC 2-30/7.5-350-H2 | 30 | 7.5 | 350 | 18.5 | 1750 |
DC 2-25/7.5-400-H2 | 25 | 7.5 | 400 | 18.5 | 1750 |
DC 2-55/9-200-H2 | 55 | 9 | 200 | 18.5 | 1750 |
DC 2-65/10-150-H2 | 65 | 10 | 150 | 22 | 1750 |
DC 2-54/10-200-H2 | 54 | 10 | 200 | 18.5 | 1750 |
DC 2-50/10-250-H2 | 50 | 10 | 250 | 18.5 | 1750 |
DC 2-50/10-270-H2 | 50 | 10 | 270 | 18.5 | 1750 |
DC 2-40/10-300-H2 | 40 | 10 | 300 | 18.5 | 1750 |
DC 2-40/10-350-H2 | 40 | 10 | 350 | 18.5 | 1750 |
DC 2-28/10-350-H2 | 28 | 10 | 350 | 15 | 1750 |
DC 2-25/10-400-H2 | 25 | 10 | 400 | 18.5 | 1750 |
DC 2-35/10-400-H2 | 35 | 10 | 400 | 22 | 1750 |
DC 2-80/14-160-H2 | 80 | 14 | 160 | 18.5 | 1750 |
DC 2-60/14-350-H2 | 60 | 14 | 350 | 18.5 | 1750 |
DC 2-65/15-250-H2 | 65 | 15 | 250 | 18.5 | 1750 |
DC 2-40/15-400-H2 | 40 | 15 | 400 | 18.5 | 1750 |
DC 2-110/25-200-H2 | 110 | 25 | 200 | 22 | 1750 |
DC 2-240/150-400-H2 | 240 | 150 | 400 | 18.5 | 1750 |
DC 3-60/0.1-165-H2 | 60 | 0.1 | 165 | 37 | 4500 |
DC 3-70/0.5-100-H2 | 70 | 0.5 | 100 | 37 | 4500 |
DC 3-120/5-150-H2 | 120 | 5 | 150 | 45 | 4500 |
DC 3-110/5-250-H2 | 110 | 5 | 250 | 45 | 4500 |
DC 3-142/6-250-H2 | 142 | 6 | 250 | 45 | 4500 |
DC 3-60/7-160-H2 | 60 | 7 | 160 | 37 | 4500 |
DC 3-350/25-200-H2 | 350 | 25 | 200 | 55 | 4500 |
DC 4-150/5-250-H2 | 150 | 5 | 250 | 55 | 8600 |
DC 4-200/5-250-H2 | 200 | 0.5 | 250 | 75 | 8600 |
DC 10-7/10-700-H2 | 7 | 10 | 700 | – | – |
DC 10-5/8-700-H2 | 5 | 8 | 700 | – | – |
DC 10-15/50-900-H2 | 15 | 50 | 900 | – | – |
DC 10-85/20-900-H2 | 85 | 20 | 900 | – | – |
Pressures 1000 bar g and more are under request.
That’s all.
If you need any help please don’t hesitate to contact us:
Also you can see our realized projects here
Best regards
Konstantin Shirokikh